Show us your pneumatic spud gun! Discuss pneumatic (compressed gas) powered potato guns and related accessories. Valve types, actuation, pipe, materials, fittings, compressors, safety, gas choices, and more.
-
Leonard
- Private 4
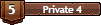
- Posts: 93
- Joined: Fri Feb 08, 2008 1:38 am
Sat Mar 14, 2009 4:03 pm
Hello guys!
I am in the process of building a blow-back hammer valve pneumatic launcher (copy of spyder's valve and bolt setup : stacked tube type). I must say i dont post here very often, but i would need the help of experienced member for something. I promise in return i will post the results, and i am quite positive about them.
Here's a link to the actual setup i plan to reproduce :
My main problem is the rear bolt, the one that hits the hammer. It obviously need a perfect seal in front of it in order the achieve semi-auto (as seen by the o-ring in the animation). Howhere, i do not have access to a lathe. I was wondering if a floating O-ring (as seen in
http://www.spudfiles.com/forums/easy-st ... 13277.html) could do the job. Im concerned that the floating o-ring is made for use in a pump and may not work for this type of application.
I am also aware that there will be a lot of work to do in order to tune the springs tensions and pressure, but i got a lot of patience ^-^
Thanks in advance guys!
-
Gippeto
- First Sergeant 3
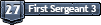

- Posts: 2503
- Joined: Sat Jan 19, 2008 10:14 am
- Location: Soon to be socialist shit hole.
- Has thanked: 2 times
- Been thanked: 17 times
Sat Mar 14, 2009 6:49 pm
If close tolerances were maintained, I don't think you even need an o-ring on the hammer. The portion of gas in question is vented off right away anyway.
Something that fits closely, should work fine.
Off the top of my head, a mixture of epoxy and metal filler casted in the tube? Use lead shot or steel filings as the filler to add weight.
"It could be that the purpose of your life is to serve as a warning to others" – unknown
Liberalism is a mental disorder, reality is it's cure.
-
inonickname
- First Sergeant 4
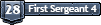
- Posts: 2606
- Joined: Sun Dec 07, 2008 3:27 am
Sat Mar 14, 2009 7:12 pm
Here's a simpler design:
Here
The main difference is that there is potential to waste a bit more air, but mine will be simpler to get working.
Ohh..you only want semi. That design is nothing away from full automatic, so keep that in mind.
Try using a drill press and a wood chisel chucked in the vice to machine the piston (credits to the guys that made that balanced piston launcher). You probably don't need an airtight seal, just fair tolerances.
PimpAssasinG wrote:no im strong but you are a fat gay mother sucker that gets raped by black man for fun
-
Leonard
- Private 4
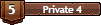
- Posts: 93
- Joined: Fri Feb 08, 2008 1:38 am
Sat Mar 14, 2009 7:36 pm
Humn! That surprise me. I was realy sure i needed to go for full airtighness. It will certainly make everything easier.
If i may ask, Gippeto, you were mentionning a need for a heavy construction of the hammer, do you think that a 3 centimeters long jb weld cast bolt would be sufficiently heavy? I am looking into using relatively high pressures (~250 psi), so i am expecting the valve to be hard to open.
-
psycix
- Sergeant Major 4
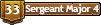
- Posts: 3684
- Joined: Mon Jun 25, 2007 7:12 am
- Location: The Netherlands
Sat Mar 14, 2009 7:41 pm
It may be just me, but a blowback will be very hard to make without a lathe.
You can try a floating o-ring. When done well it will probably seal good enough, if not perfect.
What pressure will you use this at? The point with lower pressures is that the hammer doesnt get enough speed to get back to the trigger unless the spring was weak. But that would cause another problem: the hammer not having enough power to smack the valve.
-
Leonard
- Private 4
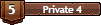
- Posts: 93
- Joined: Fri Feb 08, 2008 1:38 am
Sat Mar 14, 2009 7:48 pm
Thanks for the comment, can you point out wich part will be hard to make without a lathe? Of course if i would want an airtight construction on the upper bolt i would need a lathe to make o-ring grooves into it. But im using telescopic brass tube wich fit perfecly into each other, they are certainly not airtight, but leak will be minimal.
EDIT : I will be using around 250 psi (Reged c02).
-
psycix
- Sergeant Major 4
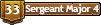
- Posts: 3684
- Joined: Mon Jun 25, 2007 7:12 am
- Location: The Netherlands
Sat Mar 14, 2009 7:52 pm
You dont NEED a lathe to make o-ring grooves. People have done it other ways. Just improvise.
-
Leonard
- Private 4
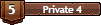
- Posts: 93
- Joined: Fri Feb 08, 2008 1:38 am
Sat Mar 14, 2009 7:55 pm
That is true. Then, you were mentionning that the construction would be hard without a lathe. I was just curious to know wich part would be easier to build with a lathe considering i will not need to make any o-ring grooves.
Basicly, im trying to figure out every part of the building process in wich i might have trouble with before going out and buying everything ^_^
-
Gippeto
- First Sergeant 3
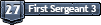

- Posts: 2503
- Joined: Sat Jan 19, 2008 10:14 am
- Location: Soon to be socialist shit hole.
- Has thanked: 2 times
- Been thanked: 17 times
Sun Mar 15, 2009 11:14 am
[quote][/If i may ask, Gippeto, you were mentionning a need for a heavy construction of the hammer, do you think that a 3 centimeters long jb weld cast bolt would be sufficiently heavy? I am looking into using relatively high pressures (~250 psi), so i am expecting the valve to be hard to open.quote]
It's the momentum of the hammer that will both open the valve, and re-cock the action. Mass is needed.
I don't think a hammer made from "just" JB Weld will have enough mass to accomplish the job.
But then, you could always just try it and find out eh? 250 psi isn't that much really.(49 pounds of force required to crack a 1/2" valve @ 250psi)
"It could be that the purpose of your life is to serve as a warning to others" – unknown
Liberalism is a mental disorder, reality is it's cure.
-
SPG
- Specialist 3
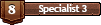
- Posts: 364
- Joined: Thu Feb 09, 2006 11:55 am
Sun Mar 15, 2009 3:52 pm
psycix wrote:It may be just me, but a blowback will be very hard to make without a lathe.
You can try a floating o-ring. When done well it will probably seal good enough, if not perfect.
What pressure will you use this at? The point with lower pressures is that the hammer doesnt get enough speed to get back to the trigger unless the spring was weak. But that would cause another problem: the hammer not having enough power to smack the valve.
Not strictly true, it's all to do with spring rates. See
HERE. It should be perfectly possible to build the right system to allow decent hammer travel without too weak a spring. We can do it by building a constant rate spring.
-
Leonard
- Private 4
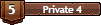
- Posts: 93
- Joined: Fri Feb 08, 2008 1:38 am
Mon Mar 16, 2009 6:15 pm
Thanks for the comments and input guys. I have began building today, wish me luck!
Oh, and do you think i should it put up a build log? Would there be any interest?
-
jackssmirkingrevenge
- Five Star General
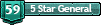
- Posts: 26189
- Joined: Thu Mar 15, 2007 11:28 pm
- Has thanked: 551 times
- Been thanked: 328 times
Mon Mar 16, 2009 6:21 pm
Leonard wrote:Oh, and do you think i should it put up a build log? Would there be any interest?
Please do
Actually, this has given me a rather crazy idea in conjunction with my thoughts of a
micro BBMG.
I had already thought up a vaguely similar design of a blowback hammer valve auto
here.
How about scale this down to 3mm calibre, and use a cut down schrader as a ready made hammer valve
I think I have me a new project...
-
SPG
- Specialist 3
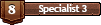
- Posts: 364
- Joined: Thu Feb 09, 2006 11:55 am
Tue Mar 17, 2009 5:05 am
Jack, why bother cutting down a schraeder, just use a presta instead.