Two stage fridge compressor build
Hey Guys,
First I want to say thank you for all the input and advice regarding my compressor. I finally have decided on a design and have bought most components. I do not have much to show as of yet. But, I will take pictures over the next week or so to show you.
The layout is as follows;
Two refrigerator compressors-- One charges a 3 gallon air tank to 200 psi (a truck air horn tank). This 200 psi is regulated down to the input of the second compressor. I am installing an unloading valve on the feed line to the tank to help with compressor restart, and there will be a solenoid valve between the tank and the second stage compressor. The high pressure output (up to 800 psi) will be fed to the cannon directly from the compressor to the cannon. That feed will consist of a braided stainless dishwasher inlet line. Those lines are rated for 1,700 psi, are not too thick, are readily available, and are innexpensive. The the hose will terminate at the end with another small solenoid valve. This valve will be open when the second stage compressor is running and closed when the second stage compressor shuts off. The reason for this valve is to aid in disconnecting the fill line from the cannon. At 800 psi, the air in the hose has alot of energy. When disconnecting that hose, the air discharge is loud and very hard to hold onto. The hose wants to jump out of my hand. So, that tiny solenoid valve (brass high pressure valve) will shut off when the compressor is shut down and only a tiny amount of air will be left to pop when the line is disconnected. There will be blow off valves, pressure switches, and other safetys built in. It will be a bit on a complicated side, but I want this compressor built right and I want it to work properly.
The compressor unit as a whole will have a cage welded from one inch box section steel tube with a control console angle mounted at the top. The console will have a main power switch, 4 guages (one for the tank pressure, one for the regulated output to the second stage compressor, one for a regulated output of the tank for tools and lower pressure cannons, and one 1,000 psi guage for the high pressure output). There will be one regulated output quick disconnect on the console, one unregulated disconnect (170-200 psi from the tank), and the high pressure line from the output of the second stage compressor. All regulators, quick disconnects, guages, and switches will be asthetically layed out and easy to see. The console itself will be either anodized aluminum or stained and finished wood. The frame will be powder coated black. My goal is to make this compressor very finished looking, easy to use, and very safe.
I have nearly everything on-hand for it and I will post pictures as I have them.
Matt
First I want to say thank you for all the input and advice regarding my compressor. I finally have decided on a design and have bought most components. I do not have much to show as of yet. But, I will take pictures over the next week or so to show you.
The layout is as follows;
Two refrigerator compressors-- One charges a 3 gallon air tank to 200 psi (a truck air horn tank). This 200 psi is regulated down to the input of the second compressor. I am installing an unloading valve on the feed line to the tank to help with compressor restart, and there will be a solenoid valve between the tank and the second stage compressor. The high pressure output (up to 800 psi) will be fed to the cannon directly from the compressor to the cannon. That feed will consist of a braided stainless dishwasher inlet line. Those lines are rated for 1,700 psi, are not too thick, are readily available, and are innexpensive. The the hose will terminate at the end with another small solenoid valve. This valve will be open when the second stage compressor is running and closed when the second stage compressor shuts off. The reason for this valve is to aid in disconnecting the fill line from the cannon. At 800 psi, the air in the hose has alot of energy. When disconnecting that hose, the air discharge is loud and very hard to hold onto. The hose wants to jump out of my hand. So, that tiny solenoid valve (brass high pressure valve) will shut off when the compressor is shut down and only a tiny amount of air will be left to pop when the line is disconnected. There will be blow off valves, pressure switches, and other safetys built in. It will be a bit on a complicated side, but I want this compressor built right and I want it to work properly.
The compressor unit as a whole will have a cage welded from one inch box section steel tube with a control console angle mounted at the top. The console will have a main power switch, 4 guages (one for the tank pressure, one for the regulated output to the second stage compressor, one for a regulated output of the tank for tools and lower pressure cannons, and one 1,000 psi guage for the high pressure output). There will be one regulated output quick disconnect on the console, one unregulated disconnect (170-200 psi from the tank), and the high pressure line from the output of the second stage compressor. All regulators, quick disconnects, guages, and switches will be asthetically layed out and easy to see. The console itself will be either anodized aluminum or stained and finished wood. The frame will be powder coated black. My goal is to make this compressor very finished looking, easy to use, and very safe.
I have nearly everything on-hand for it and I will post pictures as I have them.
Matt
Last edited by High-PSI on Wed Dec 28, 2011 9:14 pm, edited 2 times in total.
Exotic E-bike builder, air cannon builder, and overall crack-pot. ;~)
Understood. If you look, you will notice the secondary compressor is fed with a regulated output. The reason the tank is 200 psi is for higher capacity with a 3 gallon tank. Also, I have been bench testing the two stage system. It fills the cannon much faster with over 100 psi fed into the second compressor than the typical 60 psi.
I know this has been done. What I have never seen, however, is a completed unit that is easy and safe to use.
Matt
I know this has been done. What I have never seen, however, is a completed unit that is easy and safe to use.
Matt
Exotic E-bike builder, air cannon builder, and overall crack-pot. ;~)
Zeus wrote:Feeding fridge compressors like that has been done, but with a shop compressor with the reg set at 60PSI.
i searched that, but with no good results, correct me if i am wrong, but aren't you basically saying that i could put 60psi into the input of a fridge compressor, and get out over 200? please explain this to me, i am looking for a way to obtain a high pressure air compressing system. i already have a fridge compressor and a very capable shop compressor, could i simply combine them for an efficient high pressure system?
- Gun Freak
- Lieutenant 5
- Posts: 4971
- Joined: Mon Jan 25, 2010 4:38 pm
- Location: Florida
- Been thanked: 7 times
A fridgy can already get over 200 psi, a pressurized input just makes it go faster and be able to go higher.
OG Anti-Hybrid
One man's trash is a true Spudder's treasure!
Golf Ball Cannon "Superna" ■ M16 BBMG ■ Pengun ■ Hammer Valve Airsoft Sniper ■ High Pressure .22 Coax
Holy Shat!
One man's trash is a true Spudder's treasure!
Golf Ball Cannon "Superna" ■ M16 BBMG ■ Pengun ■ Hammer Valve Airsoft Sniper ■ High Pressure .22 Coax
Holy Shat!
Depending on the compressor, you can get upwards of 500 psi out of one fridge compressor. If you feed the input with 80 psi, you can see over 800 psi of output (again, depending on the type of compressor). There are some specifics you need to know about this to do it properly, but it does work.
Matt
Matt
Exotic E-bike builder, air cannon builder, and overall crack-pot. ;~)
- Fnord
- First Sergeant 2
- Posts: 2239
- Joined: Tue Feb 13, 2007 9:20 pm
- Location: Pripyat
- Been thanked: 1 time
- Contact:
I'd think that you would want a higher volume compressor for the primary stage. Fridge compressors aren't really designed for anything that big so it would probably take a while. You could salvage a small shop compressor and either change the pulleys or put a bigger motor on it to achieve the desired 200psi.
You'll also have the benefit of the shop compressor putting oil into the system, which will extend the life of your fridgy.
You'll also have the benefit of the shop compressor putting oil into the system, which will extend the life of your fridgy.
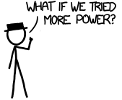
Yes, I agree. However, it only takes 6 minutes for my fridge compressor to charge the 3 gallon take to 200 psi. Also, fridge compressors put a small amount of oil into a system anyway.
I have a decent shop compressor. But, I want this unit to be silent. I will make the primary stage twin compressors if I need to. I think this will be fine, though.
Matt
I have a decent shop compressor. But, I want this unit to be silent. I will make the primary stage twin compressors if I need to. I think this will be fine, though.
Matt
Exotic E-bike builder, air cannon builder, and overall crack-pot. ;~)
I did some more testing today. With a regulated 75 psi running to the input of my second stage compressor, I saw exactly 800 psi at the output of the second stage before the second stage compressor stalled out. So, I assume 100 psi input would net 1,000 psi at the output. That being said, I do not plan on using any more than 800 psi. So, this was a good test.
Also, I went to the hardware store and found the perfect high pressure feed line. It is a braided stainless icemaker line. It has 1/4 compression fittings at the ends and is relatively narrow. That is the line I did the 800 psi test with. It works well and looks good.
I also picked up my steel for the compressor frame. The compressor frame will measure 24 inches long by 15 inches wide and 12 inches high. This thing will weigh a ton. Two fridge compressors and all the fittings are freakin heavy.
Matt
Also, I went to the hardware store and found the perfect high pressure feed line. It is a braided stainless icemaker line. It has 1/4 compression fittings at the ends and is relatively narrow. That is the line I did the 800 psi test with. It works well and looks good.
I also picked up my steel for the compressor frame. The compressor frame will measure 24 inches long by 15 inches wide and 12 inches high. This thing will weigh a ton. Two fridge compressors and all the fittings are freakin heavy.
Matt
Exotic E-bike builder, air cannon builder, and overall crack-pot. ;~)
- mark.f
- Sergeant Major 4
- Posts: 3628
- Joined: Sat May 06, 2006 11:18 am
- Location: The Big Steezy
- Has thanked: 52 times
- Been thanked: 53 times
- Contact:
That hose is what I used on my homemade pump and pilot line on my copper pneumatic, it does work really, really well, and can be taken off fairly easily thanks to the compression connections.High-PSI wrote:I did some more testing today. With a regulated 75 psi running to the input of my second stage compressor, I saw exactly 800 psi at the output of the seconAlso, I went to the hardware store and found the perfect high pressure feed line. It is a braided stainless icemaker line. It has 1/4 compression fittings at the ends and is relatively narrow. That is the line I did the 800 psi test with. It works well and looks good.
I do not have any good pictures to show yet. I have been doing technical testing of all components and the system as a whole (bench testing). The system is working well. I installed a normally open solenoid valve on a "T" from the primary compressor to tank line. This unloads the pressure from that line when the compressor shuts down, thus allowing the compressor to start back up with required.
When I tested the compressor with repeated restarting and refilling of the tank (worse case scinerio) I found that after 5 consecutive tank refills, the compressor was 153 degrees and thermaled off. So, I added a 4 inch box fan to blow on the side of the compressor and repeated the test (after letting the compressor cool off fully). This time I drained and recharged the tank 13 times and was only at 142 degrees! That is with the fan set to run only when the compressor was running. If it ran 100% of the time, the temp would be even lower. Also, it never went over 143 degrees. That seems to be the max temp with the fan.
I will report back and post pictures when I can.
Matt
When I tested the compressor with repeated restarting and refilling of the tank (worse case scinerio) I found that after 5 consecutive tank refills, the compressor was 153 degrees and thermaled off. So, I added a 4 inch box fan to blow on the side of the compressor and repeated the test (after letting the compressor cool off fully). This time I drained and recharged the tank 13 times and was only at 142 degrees! That is with the fan set to run only when the compressor was running. If it ran 100% of the time, the temp would be even lower. Also, it never went over 143 degrees. That seems to be the max temp with the fan.
I will report back and post pictures when I can.
Matt
Exotic E-bike builder, air cannon builder, and overall crack-pot. ;~)
I think you'll find that making the input pressure higher won't raise the output pressure any more by a significant amount. In some cases the compressor will stall (or trip the current limiting switch) even before max pressure is reached.
Probably so. In any event, I reached 800 psi with 80 psi input. That is all I need. I would like to hit 1,000 psi output, however, just to know it can do it and that I am not hitting its absolute limit every time I charge my gun to 800.al-xg wrote:I think you'll find that making the input pressure higher won't raise the output pressure any more by a significant amount. In some cases the compressor will stall (or trip the current limiting switch) even before max pressure is reached.
Matt
Exotic E-bike builder, air cannon builder, and overall crack-pot. ;~)
Here are some pictures of the compressor as is sits. I hope to have the framework and all other fabrication finished by the weekend so I can get it to the powder-coater for some color.
The console is, obviously, the protruding rectangle at the front/top. All controls, regulators, switches, guages, and quick disconnects will be located there.
Matt
The console is, obviously, the protruding rectangle at the front/top. All controls, regulators, switches, guages, and quick disconnects will be located there.
Matt
Exotic E-bike builder, air cannon builder, and overall crack-pot. ;~)