
Building a pistol grip?
- Gippeto
- First Sergeant 3
- Posts: 2504
- Joined: Sat Jan 19, 2008 10:14 am
- Location: Soon to be socialist shit hole.
- Has thanked: 2 times
- Been thanked: 17 times
"It could be that the purpose of your life is to serve as a warning to others" – unknown
Liberalism is a mental disorder, reality is it's cure.
Liberalism is a mental disorder, reality is it's cure.
I drilled and tapped two holes to mount the blowgun to plates which were later welded to a barrel.
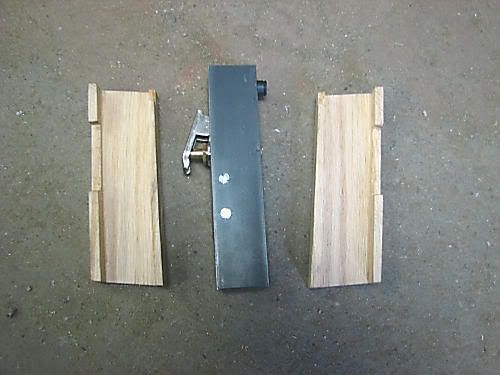
This one was a little more complex. This is a piece of 1.5 tubing, egged with a hammer. A grip plate was weld onto the bottom with a hole drilled in it. A bolt is inserted and passes up behind the blowgun and screws into the housing of the flame tube. The blowgun is precisely fitted so it is free floating and does not move. Remove the retaining bolt, and you have instant access to the blowgun and push to connect fittings with 1/4" tubing.
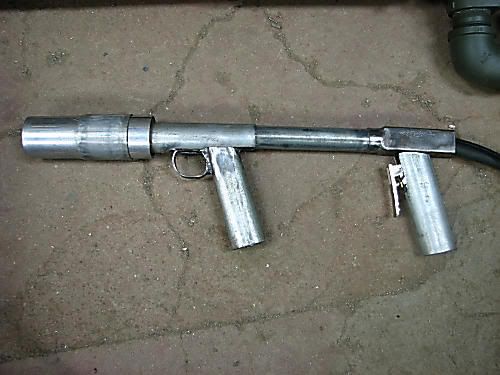
///ed///
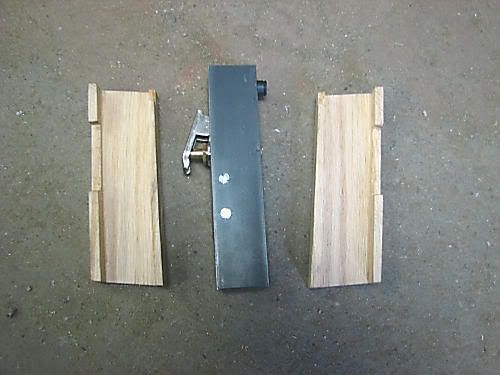
This one was a little more complex. This is a piece of 1.5 tubing, egged with a hammer. A grip plate was weld onto the bottom with a hole drilled in it. A bolt is inserted and passes up behind the blowgun and screws into the housing of the flame tube. The blowgun is precisely fitted so it is free floating and does not move. Remove the retaining bolt, and you have instant access to the blowgun and push to connect fittings with 1/4" tubing.
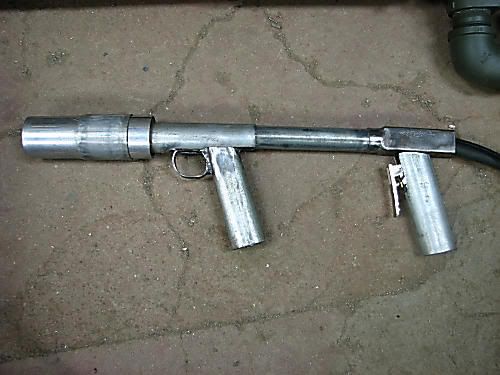
///ed///
Use foam and fibreglass, it's really easy and has been used to make composite stocks for proper airguns and small calibre fire-arms.
You'll need some of the blue insulating foam sheet for preference, it's quite solid (doesn't flake like expanded polystyrene) but it cuts very easily with a craft knife, carving knife, or spend a few bucks and get a hot-wire.
In the past what I've done is made stocks by laminating three or more sheets together, I always aim to get the middle sheet the same thickness as any components within the stock, that way you can cut out the holes for them and seat them nicely. Then glue the other two sheets either side to hold things in place. If you want things very solidly mounted then you can laminate in steel reinforcement between the layers, and run pins or bolts through the whole lot.
You can then either lay a few of layers of fibreglass over the top for solidity, or you could just bondo, it won't be as solid, but it's quicker.
The great thing is cell-core insulation foam is cheap, and you get a lot of it so you can make plenty of mistakes (err design adjustments).
You'll need some of the blue insulating foam sheet for preference, it's quite solid (doesn't flake like expanded polystyrene) but it cuts very easily with a craft knife, carving knife, or spend a few bucks and get a hot-wire.
In the past what I've done is made stocks by laminating three or more sheets together, I always aim to get the middle sheet the same thickness as any components within the stock, that way you can cut out the holes for them and seat them nicely. Then glue the other two sheets either side to hold things in place. If you want things very solidly mounted then you can laminate in steel reinforcement between the layers, and run pins or bolts through the whole lot.
You can then either lay a few of layers of fibreglass over the top for solidity, or you could just bondo, it won't be as solid, but it's quicker.
The great thing is cell-core insulation foam is cheap, and you get a lot of it so you can make plenty of mistakes (err design adjustments).
<A HREF="http://www.paisleypeking.co.uk"><IMG BORDER="0" WIDTH="400" HEIGHT="64" SRC="http://www.paisleypeking.co.uk/images/s ... e.gif"></A>