
Was about to ask myself actually so this works well, But I'm not sure if turning a shoulder into the piston behind the barrel seal would be very ideal. The surface area on the barrel side isn't far off that of the pilot side. The surface area of a little less than the m10 is the only difference. Do you think it will actuate fast enough? Seems you would need a serious pilot valve for that to work better than something like a low ratio piston valve.
That and if you make it from engineering plastic, you really don't save that much weight from turning the shoulder. On a 55mm x 57mm piston Only about 40 grams out of 215 total would be saved, that's with delrin which is one of the heaviest plastics.
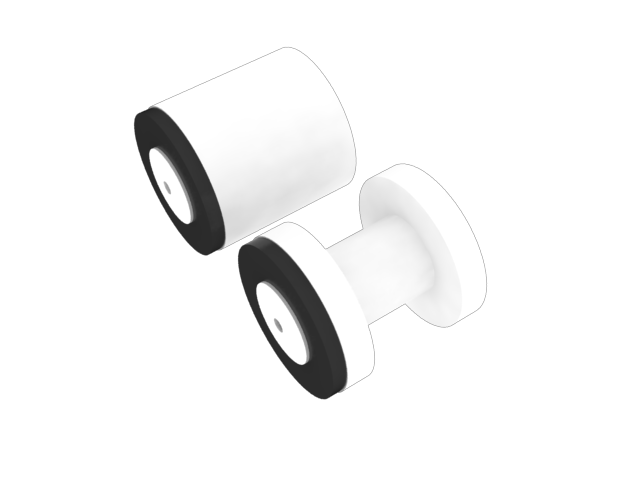
What i was thinking of doing was turning a large recess between the two o rings on the piston so the area on either side of the recess is equal, cancelling the net force out. That would save much more weight, keep the surface area of the barrel side small for quicker valve actuation and probably be easier to make.
However what I'm not sure of is how the pressurised air between the o rings would effect the piston operation. When the valves fired it would basically stay pressurised minus leakage through the equaliser port (or completely pressurised with a check valve). Would it slow the piston down or what? Or is it just "dead volume" that doesn't affect anything?
With your tolerance question (forgive me if i'm reading this all wrong i kinda glanced over this page lol) I made the piston about .025mm underiszed in diameter which let it drop slowly through the tube under gravity. Even then it had too much leakage to work as a piston valve but works good with an oring, because the plastic piston can still take the load if it has to, meaning you only need one o ring = lighter piston.
The O ring diameter i used was 3.25mm and i think the slot it sits in is roughly 3.2mm deep. I'll have to double check it though! In any case its not extending very far. A firm push with two fingers can move the piston though as an indicator.
As for material and what not, I guess NZ would be pretty similar to Aus. The only o-rings i can find are in those kits jackssmirkingrevenge mentioned. But even then there aren't really that many sizes. the biggest is 32mm radius and the one under that is 31mm, neither of which fit into any metric pvc locally without stretching.
Best thing you can do is buy this stuff from mcmaster
http://www.mcmaster.com/#urethane-round-belts/=hn39qr
which unfortunately you can only buy if you have an account with them (i know someone that does luckily


As for plastics there is a place in melbourne that is very cheap. Got a 1m long piece of 80mm diameter delrin for $1 per cm. $1.50 per cm shipped to Sydney. Most "engineering" stores or bearing stores retail it from cut to size plastics or dotmar in Aus. Perhaps NZ has the same buisinesses?
But yeah man if you wan't anything machined or some materials sent over let me know hey
