Short question topic
- MrCrowley
- Moderator
- Posts: 10078
- Joined: Fri Jun 23, 2006 10:42 pm
- Location: Auckland, New Zealand
- Been thanked: 3 times
Ah I see, it's probably a bit more difficult to grasp when your sealing face is larger than the piston diameter.
For the sealing face part of the piston, you'll have roughly ~7cm^3 of area for pressure to push the piston forward. This is assuming your piston is a rod piston similar to mine where the sealing face part is separated from the o-ring part of the piston. The area left remaining on the sealing face that is not taken up by the seat is roughly ~1.7cm^3 and then (again, assuming the piston is similar to mine and that the back of piston is the same diameter as the front of the piston (not the sealing face part)) another 4.15cm^3 pushing back the front part of the piston (not the sealing face part).
This comes to a total of 7cm^3 pushing the piston forward with ~5.8cm^3 pushing the piston back.
For the back part you'll have ~4cm^3 pushing it forward (minus the bolt area of ~0.2cm^3) with 1.3cm^3 pushing the piston back.
The reason I have separated the calculations in to "front" and "back" is because if your design is like mine, the pre-ignition chamber pressure is different from the pilot pressure. So while the back of the piston may have 300PSI acting on it, the sealing face may only have a pre-ignition pressure of 132PSI acting on it.
Take my math and calculations for granted, I didn't bother much with carrying significant figures. I'm also assuming your piston is configured like mine. If the piston was a solid body like I'm planning on getting you to machine for me, it's a little easier to calculate as you don't have to worry about pressure acting on the back part of the sealing face.
For the sealing face part of the piston, you'll have roughly ~7cm^3 of area for pressure to push the piston forward. This is assuming your piston is a rod piston similar to mine where the sealing face part is separated from the o-ring part of the piston. The area left remaining on the sealing face that is not taken up by the seat is roughly ~1.7cm^3 and then (again, assuming the piston is similar to mine and that the back of piston is the same diameter as the front of the piston (not the sealing face part)) another 4.15cm^3 pushing back the front part of the piston (not the sealing face part).
This comes to a total of 7cm^3 pushing the piston forward with ~5.8cm^3 pushing the piston back.
For the back part you'll have ~4cm^3 pushing it forward (minus the bolt area of ~0.2cm^3) with 1.3cm^3 pushing the piston back.
The reason I have separated the calculations in to "front" and "back" is because if your design is like mine, the pre-ignition chamber pressure is different from the pilot pressure. So while the back of the piston may have 300PSI acting on it, the sealing face may only have a pre-ignition pressure of 132PSI acting on it.
Take my math and calculations for granted, I didn't bother much with carrying significant figures. I'm also assuming your piston is configured like mine. If the piston was a solid body like I'm planning on getting you to machine for me, it's a little easier to calculate as you don't have to worry about pressure acting on the back part of the sealing face.
- Crna Legija
- First Sergeant 2
- Posts: 2333
- Joined: Sun Jul 20, 2008 5:14 am
- Location: australia
well yeah its just like your piston i think.


'' To alcohol... The cause of, and solution to, all of life's problems.”
--Homer Simpson
Add me on ps3: wannafuk, 8/11/11 cant wait
--Homer Simpson
Add me on ps3: wannafuk, 8/11/11 cant wait
- MrCrowley
- Moderator
- Posts: 10078
- Joined: Fri Jun 23, 2006 10:42 pm
- Location: Auckland, New Zealand
- Been thanked: 3 times
Yeah so a diagram of the forces will look something like this:
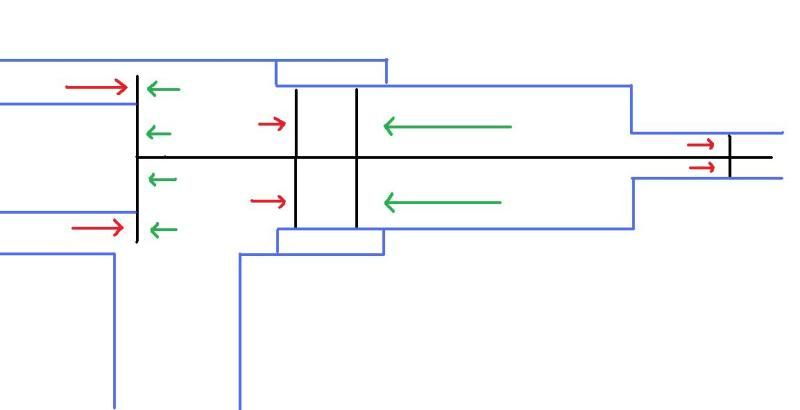
Just remember to account for the pre-ignition chamber pressure for the front part of the piston like I mentioned earlier.
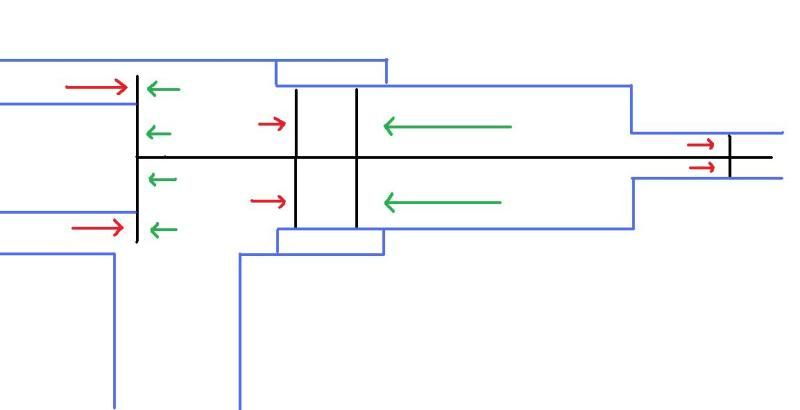
Just remember to account for the pre-ignition chamber pressure for the front part of the piston like I mentioned earlier.
- Crna Legija
- First Sergeant 2
- Posts: 2333
- Joined: Sun Jul 20, 2008 5:14 am
- Location: australia
ohh kool never thought about the front part like that thanks.
I tried to work it out, i think it might be wrong i came up with 512 psi in pilot for a 10x shot, I don't know why but it seams high. ill give it a shot this week end but at 5x with only 256 in the pilot, hope its not too loud.
I tried to work it out, i think it might be wrong i came up with 512 psi in pilot for a 10x shot, I don't know why but it seams high. ill give it a shot this week end but at 5x with only 256 in the pilot, hope its not too loud.
'' To alcohol... The cause of, and solution to, all of life's problems.”
--Homer Simpson
Add me on ps3: wannafuk, 8/11/11 cant wait
--Homer Simpson
Add me on ps3: wannafuk, 8/11/11 cant wait
- wyz2285
- First Sergeant 2
- Posts: 2388
- Joined: Sat Mar 06, 2010 7:50 am
- Location: Porto, Portugal
- Has thanked: 1 time
- Been thanked: 4 times
- Contact:
I was simulating using Autodesk Inventor Professional (student version) a chamber for my pcp, but I think I have done something wrong
Material: stainless steel, 440C
length: 10 inch
OD: 1 inch
Wall: 1 inch
Pressure: 3750psi (250bar)
It shows a minim safety factor of about 2, but I can see the chamber gets deformed quite noticeably
I´m pretty sure that I did something stupid
I´m studing how to use Autodesk Simulation Multiphysics, but haven´t be able to use it effectivelly yet.
A picture of what I´m trying to do. The model it´s just a cylinder, I made it just to see how the simulation works. I can create parts far better than that

Material: stainless steel, 440C
length: 10 inch
OD: 1 inch
Wall: 1 inch
Pressure: 3750psi (250bar)
It shows a minim safety factor of about 2, but I can see the chamber gets deformed quite noticeably


I´m studing how to use Autodesk Simulation Multiphysics, but haven´t be able to use it effectivelly yet.
A picture of what I´m trying to do. The model it´s just a cylinder, I made it just to see how the simulation works. I can create parts far better than that

Last edited by wyz2285 on Wed May 23, 2012 3:15 pm, edited 1 time in total.
CpTn_lAw wrote:"yay, me wanna make big multishot pnoob with 1000 psi foot pump compressor using diamond as main material. Do you think wet bread make good sealant? "
![]()
- POLAND_SPUD
- Captain
- Posts: 5402
- Joined: Sat Oct 13, 2007 4:43 pm
- Been thanked: 1 time
uhmm IIRC that's perfectly normal - the program presents them in this blown out of proportion way so that they are easier to notice
Children are the future
unless we stop them now
unless we stop them now
- wyz2285
- First Sergeant 2
- Posts: 2388
- Joined: Sat Mar 06, 2010 7:50 am
- Location: Porto, Portugal
- Has thanked: 1 time
- Been thanked: 4 times
- Contact:
Ah that makes sense, because when I did the same simulation in multiphysics, nothing happened. Well anyway safety factor (in yield strength) 2 isn't safe enough but 0.15 inch wall thickness brings the minimum safety factor to around 4, so I'm pretty sure about the chamber size/material now.
CpTn_lAw wrote:"yay, me wanna make big multishot pnoob with 1000 psi foot pump compressor using diamond as main material. Do you think wet bread make good sealant? "
![]()
- MrCrowley
- Moderator
- Posts: 10078
- Joined: Fri Jun 23, 2006 10:42 pm
- Location: Auckland, New Zealand
- Been thanked: 3 times
Wait a tick... will it even work if your sealing face is larger than the piston diameter? When I was trying to work it out, I calculated more area would hold the piston forward than push it back for the 'chamber pressure' calculations (rear of sealing face = 0.42in^3 vs. front of sealing face + front of piston = 0.36in^3), so when the fuel combusts the piston wont budge. You could either: (1) reduce the sealing face to about 27mm in diameter, (2) make the piston diameter larger, or (3) make the seat smaller than the piston diameter.Crna Legija wrote:ohh kool never thought about the front part like that thanks.
I tried to work it out, i think it might be wrong i came up with 512 psi in pilot for a 10x shot, I don't know why but it seams high. ill give it a shot this week end but at 5x with only 256 in the pilot, hope its not too loud.
Try and get, what I term, a low-ratio piston where the 'pushing back' (I call this "negative area") area for the front parts of the piston is only slightly larger than the "positive area" for the front parts of the piston that help push it forward. So say for instance it was the other way round and you had .42in^3 of "negative area" vs .36"^3 of "positive area" in the front part of the piston, at a 10x mix you have ~440 pounds per square inch vs. ~380 pounds per square inch. So then you only need enough pressure in the pilot to add (440-380) ~60 pounds per square inch of force pushing the piston forward for the combustion to peak and open the valve. During pre-ignition pressures, it will be ~58PPSI vs. ~50PPSI in the front area with the extra 60PPSI in the pilot holding the piston sealed against the barrel.
Using "negative" and "positive" just help me explain the direction in which the force is acting (pushing forward or pushing back). The "negative" forces are denoted by the red arrows in my diagram from earlier and the "positive" forces are denoted by the green arrows. Length of the arrows has no correlation to the size of the forces, I was just lazy when drawing them.
My piston is roughly as follows (for the 'frontal' calculations, ignoring the pilot):
Seat = 46.5mm
Sealing face = 48.0mm
Piston diam. = 50.0mm
Frontal Negative Area = (1.2cm^3 + 19.6cm^3) = 21.7cm^3
Frontal Positive Area = 18.1cm^3
At least, that's what's making sense to me right now.
Edit: You actually may get your valve to work if the combustion turbulences/imbalances unseat the valve.
How can you calculate approximately how many shots you'll get out of a regulated source. For example, if you have a gun that has a 5 cu. inch chamber and shoots at 120psi, how many shots would a 50 cu. inch tank at 3000psi provide. Would you just multiply the 50 cu. inch*3000psi to get 150000cu.in*psi and then a shot would use 600 cu. inch psi so you would get 250 shots? I don't think it can be this simple. What is the right way to find this out
- Crna Legija
- First Sergeant 2
- Posts: 2333
- Joined: Sun Jul 20, 2008 5:14 am
- Location: australia
dont have the time right now to read it well enough, but i get the jist of it
but would making a epoxy cylinder to make the rod the dia of the piston reducing the back of the sealing face surface area for pressure to push agianst?.
but would making a epoxy cylinder to make the rod the dia of the piston reducing the back of the sealing face surface area for pressure to push agianst?.
- Attachments
-
- mod to piston..JPG (12.25 KiB) Viewed 3568 times
'' To alcohol... The cause of, and solution to, all of life's problems.”
--Homer Simpson
Add me on ps3: wannafuk, 8/11/11 cant wait
--Homer Simpson
Add me on ps3: wannafuk, 8/11/11 cant wait
- Crna Legija
- First Sergeant 2
- Posts: 2333
- Joined: Sun Jul 20, 2008 5:14 am
- Location: australia
dam really don't wanna reduce the seat dia, because i want it to be decent with golf ball as well as smaller ammo too, right now HGDT is saying 110ms with a golf ball at 10x disk bursting at 1000psi.
'' To alcohol... The cause of, and solution to, all of life's problems.”
--Homer Simpson
Add me on ps3: wannafuk, 8/11/11 cant wait
--Homer Simpson
Add me on ps3: wannafuk, 8/11/11 cant wait
- MrCrowley
- Moderator
- Posts: 10078
- Joined: Fri Jun 23, 2006 10:42 pm
- Location: Auckland, New Zealand
- Been thanked: 3 times
Unless your chamber is pretty small I reckon you'll get a lot better than that.
You could always change the tee diameter but that means you'll need a new piston. How much investment have you put in to that piston anyway? Is it all epoxied up and what not?
You could always change the tee diameter but that means you'll need a new piston. How much investment have you put in to that piston anyway? Is it all epoxied up and what not?
- Crna Legija
- First Sergeant 2
- Posts: 2333
- Joined: Sun Jul 20, 2008 5:14 am
- Location: australia
all I spent i on this is buying a mapp torch for it, i got the fittings from work because my boss told me to throw out a box full of them i took them home lol. the piston is only lock tighted together, not hard to take apart.
you said reduce sealing face to 27mm i can do that.
you said reduce sealing face to 27mm i can do that.
'' To alcohol... The cause of, and solution to, all of life's problems.”
--Homer Simpson
Add me on ps3: wannafuk, 8/11/11 cant wait
--Homer Simpson
Add me on ps3: wannafuk, 8/11/11 cant wait
- MrCrowley
- Moderator
- Posts: 10078
- Joined: Fri Jun 23, 2006 10:42 pm
- Location: Auckland, New Zealand
- Been thanked: 3 times
Actually, I'm not sure why I said that. Maybe I used the original sealing face area outside the seat instead of the revised one when the sealing face is changed to 27mm. I just checked the back of the book where I was working it all out and there are just numbers from all over the place, including my o-ring calculations
If you make the piston diameter 27mm it would work though

If you make the piston diameter 27mm it would work though
