Hybrid Piston Valve Design
- noob of noobs
- Specialist 3
- Posts: 320
- Joined: Tue Jun 12, 2007 8:04 pm
- Location: Illinois, Skokie
Hello friends! It’s winter break for me, and so I’ve decided to make a new cannon; a hybrid piston-valve cannon. This is mostly an experimental cannon; it uses a hybrid piston valve I’ve “designed” as well as a bolt system that I think is new (but not revolutionary). So I thought I’d pass it by you guys.
The piston valve seals like a barrel sealer, pushed through the carriage by a spring. The piston will be made of fiberglass resin as in Gippeto’s stirrup pump (http://www.spudfiles.com/forums/easy-st ... 13277.html) since it’s been said to hold gasses very well at high pressure. It’ll be almost the exact same design housed in ¾” M copper, except it’ll have a sealing face at the end to seal the lip of the valve. When the gases in the chamber are ignited, the piston will be pushed back by the gas and stop when it hits the elbow at the end of the carriage (the elbow is there to hold the spring, contain the piston as it is pushed back when firing, and direct any debris and hot gas if the piston blows).
Picture is somewhere below…
Since I’m not a hybrid pro, I have a couple questions regarding the valve.
1). Is lithium/petroleum grease an okay lubricant in a hybrid?
2). Is type M copper okay in a hybrid? I know it holds really high pressure, and I don’t plan on taking the hybrid any higher than 4X with a propane-air mix, but I don’t think I’ve ever seen copper on a hybrid.
3). With maybe a tennis ball bumper, will the piston survive in the valve?
4). Will a Home Depot Metal Check valve work to seal the chamber? I hope to seal the chamber off from a gas-air hose connection with one, or is that dumb? (http://www.homedepot.com/webapp/wcs/sto ... =100152605) If it is a bad idea, what do you recommend I use?
Other than that, is there any advice, concerns, or tips you’d like to mention?
Thanks a bunch!
The piston valve seals like a barrel sealer, pushed through the carriage by a spring. The piston will be made of fiberglass resin as in Gippeto’s stirrup pump (http://www.spudfiles.com/forums/easy-st ... 13277.html) since it’s been said to hold gasses very well at high pressure. It’ll be almost the exact same design housed in ¾” M copper, except it’ll have a sealing face at the end to seal the lip of the valve. When the gases in the chamber are ignited, the piston will be pushed back by the gas and stop when it hits the elbow at the end of the carriage (the elbow is there to hold the spring, contain the piston as it is pushed back when firing, and direct any debris and hot gas if the piston blows).
Picture is somewhere below…
Since I’m not a hybrid pro, I have a couple questions regarding the valve.
1). Is lithium/petroleum grease an okay lubricant in a hybrid?
2). Is type M copper okay in a hybrid? I know it holds really high pressure, and I don’t plan on taking the hybrid any higher than 4X with a propane-air mix, but I don’t think I’ve ever seen copper on a hybrid.
3). With maybe a tennis ball bumper, will the piston survive in the valve?
4). Will a Home Depot Metal Check valve work to seal the chamber? I hope to seal the chamber off from a gas-air hose connection with one, or is that dumb? (http://www.homedepot.com/webapp/wcs/sto ... =100152605) If it is a bad idea, what do you recommend I use?
Other than that, is there any advice, concerns, or tips you’d like to mention?
Thanks a bunch!
- inonickname
- First Sergeant 4
- Posts: 2606
- Joined: Sun Dec 07, 2008 3:27 am
If that does what I think it does (remove the need for a burst disk?) then that is a very well thought out design. For filling I'd just recommend a schraeder and a BV hooked up to your propane meter.
When your choosing a grease, try burning them. Whichever wont/is the hardest to burn is your best choice.
Best of luck with it.
When your choosing a grease, try burning them. Whichever wont/is the hardest to burn is your best choice.
Best of luck with it.
- ALIHISGREAT
- Staff Sergeant 3
- Posts: 1778
- Joined: Sat Aug 25, 2007 6:47 pm
- Location: UK
if you want the piston to be pushed back by the pressure, you'll need to make the barrel sealing side a smaller diameter so more pressure will be applied to push it backwards.
or just move the barrel back further into the tee, exposing the front of the piston.
or just move the barrel back further into the tee, exposing the front of the piston.
<a href="http://www.bungie.net/stats/halo3/defau ... player=ALI H IS GREAT"><img src="http://www.bungie.net/card/halo3/ALI H IS GREAT.ashx"></a>
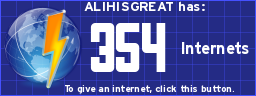
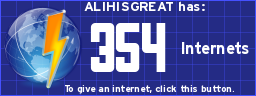
- CasinoVanart
- Specialist 2
- Posts: 281
- Joined: Wed Jul 30, 2008 1:10 am
Question two is easy, copper is fine. I use a 22mm copper tube for the barrel on my 700ml Hybrid;)
- Fnord
- First Sergeant 2
- Posts: 2239
- Joined: Tue Feb 13, 2007 9:20 pm
- Location: Pripyat
- Been thanked: 1 time
- Contact:
You need to have air pressure behind the piston (like the pilot volume in a pneumatic) , otherwise that spring is gonna need to be really strong.
1. I, personally use lithium open gear grease, but something slightly thinner is probably best. Anything flammable will mess with your mix.
2. Yes, so long as you know how to solder well. I don't know how solder will stand up to the slamming force of a heavy piston, but I know how steel did.
3. I'd use a thick hunk of rubber instead (superglue layers together if you have to). When I used a spring it was mashed up like a train had run over it.
4. If it is rated to the pressure you're using, yes. But why not use a small ball valve?
Can you give us some rough specs?
1. I, personally use lithium open gear grease, but something slightly thinner is probably best. Anything flammable will mess with your mix.
2. Yes, so long as you know how to solder well. I don't know how solder will stand up to the slamming force of a heavy piston, but I know how steel did.
3. I'd use a thick hunk of rubber instead (superglue layers together if you have to). When I used a spring it was mashed up like a train had run over it.
4. If it is rated to the pressure you're using, yes. But why not use a small ball valve?
Can you give us some rough specs?
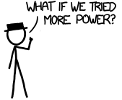
- noob of noobs
- Specialist 3
- Posts: 320
- Joined: Tue Jun 12, 2007 8:04 pm
- Location: Illinois, Skokie
Okay, so the barrel/lip will be made of 1/2" copper type L, and the piston carriage will be 3/4" type M copper. They'll be put together in a 3/4"copper T, and will connect to a smallish chamber, probably 12" of 1-1/4" Galvanized steel. The piston housing is 5" long, with about 2.5" of a steel elbow behind it to hold the spring. I don't quite know how long the piston will be, but I'm thinking the fiberglass part will be 3" or so, and the sealing face will extrude from it about 3/4" of an inch or so. I've started building the valve actually, as in a picture below...
Looking at your experiences _Fnord, I'll deffinitely look into that thick hunk of rubber (maybe get a rubber stopper from a hardware store), and am thinking a bit about a diaphram valve as proposed in your thread...
I thought I'd avoid using air cushioning just because I don't want to risk of having the "pilot" area ignite; that'd be a bit like a bomb, no? Magnet repulsion crossed my mind, but I figured it'd be a pain to attach them to a piston in any decent fashion.
Also, I'm hoping to use sprinkler valves on my metering system. That way I can operate the meter while still keeping my hands on the trigger handle. Since I didn't want to expose a sprinkler valve to a hybrid's chamber since they're rated to only 125psi, I thougth I'd use a check valve to seal the delicate valves from the destructive chamber (the check valves unfortuanately don't seem to have a pressure rating I can find). A ball valve would require more movement, and I kind of want this project to have a high rate of fire.
Also, I plan on having a burst disk in the chamber just in case the valve malfunctions and the gun turns into a bomb.
Thanks again!
Looking at your experiences _Fnord, I'll deffinitely look into that thick hunk of rubber (maybe get a rubber stopper from a hardware store), and am thinking a bit about a diaphram valve as proposed in your thread...
I thought I'd avoid using air cushioning just because I don't want to risk of having the "pilot" area ignite; that'd be a bit like a bomb, no? Magnet repulsion crossed my mind, but I figured it'd be a pain to attach them to a piston in any decent fashion.
Also, I'm hoping to use sprinkler valves on my metering system. That way I can operate the meter while still keeping my hands on the trigger handle. Since I didn't want to expose a sprinkler valve to a hybrid's chamber since they're rated to only 125psi, I thougth I'd use a check valve to seal the delicate valves from the destructive chamber (the check valves unfortuanately don't seem to have a pressure rating I can find). A ball valve would require more movement, and I kind of want this project to have a high rate of fire.
Also, I plan on having a burst disk in the chamber just in case the valve malfunctions and the gun turns into a bomb.
Thanks again!
Pistons are a dodgy thing at high pressure, capturing them is a pain in the arse.
Why not use a diaphragm valve?
Air pressure behind it can keep it shut and on firing it flexes backwards into the cup shape space you made for it to go into.
Very little mass and no problems controlling its energy.
Why not use a diaphragm valve?
Air pressure behind it can keep it shut and on firing it flexes backwards into the cup shape space you made for it to go into.
Very little mass and no problems controlling its energy.
- ALIHISGREAT
- Staff Sergeant 3
- Posts: 1778
- Joined: Sat Aug 25, 2007 6:47 pm
- Location: UK
be sure to wear hearing protection thenI plan on having a burst disk in the chamber just in case the valve malfunctions and the gun turns into a bomb.

but i doubt it will fail, in fact i fail to see how it could fail (LOL) in a way that a burst disc on the chamber would prevent? you should't be messing with pressures that your chamber can't handle

<a href="http://www.bungie.net/stats/halo3/defau ... player=ALI H IS GREAT"><img src="http://www.bungie.net/card/halo3/ALI H IS GREAT.ashx"></a>
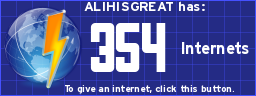
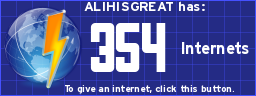
- noob of noobs
- Specialist 3
- Posts: 320
- Joined: Tue Jun 12, 2007 8:04 pm
- Location: Illinois, Skokie
Thanks for the help!
I've decided I'm going to use a diaphragm valve as recommended. I made a diagram below. I'm thinking of making it in a 1" steel T, A couple questions though:
1). Do you guys think that 4 layers of bike tube will be okay as the diaphragm?
2). Is a washer necessary? I don't plan on pushing the diaphragm into place with air, but a spring instead, so I don't think that I need a washer to keep the phram in place.
3). How big of a union do you think I need if I still plan on using a 1/2" sealing lip? I'd prefer not to make this some huge-@$$ valve, and large steel unions are pretty expensive
Again, thanks for the help!
BTW: The burst disk is just there in case the valve were to jam and trap the explosion inside the pipes. Cause' that'd be bad
I've decided I'm going to use a diaphragm valve as recommended. I made a diagram below. I'm thinking of making it in a 1" steel T, A couple questions though:
1). Do you guys think that 4 layers of bike tube will be okay as the diaphragm?
2). Is a washer necessary? I don't plan on pushing the diaphragm into place with air, but a spring instead, so I don't think that I need a washer to keep the phram in place.
3). How big of a union do you think I need if I still plan on using a 1/2" sealing lip? I'd prefer not to make this some huge-@$$ valve, and large steel unions are pretty expensive
Again, thanks for the help!
BTW: The burst disk is just there in case the valve were to jam and trap the explosion inside the pipes. Cause' that'd be bad

I would use an O-ringed piston and fill the pilot separately to a low-ish pressure. This would prevent the pilot from having air-fuel in it, and if there were no leaks, it would be nearly impossible for it to hit the elbow, if you controlled dead-space. so possibly a cap in place of the elbow. Just my $0.02, and my design for my future 1.25" porting, 3" bore 10x hybrid.
POLAND_SPUD wrote:even if there was no link I'd know it's a bot because of female name
- ALIHISGREAT
- Staff Sergeant 3
- Posts: 1778
- Joined: Sat Aug 25, 2007 6:47 pm
- Location: UK
I'm not convinced with the diaphragm idea, I think it will have disappointing performance because its effectively a coaxial combustion, and my understanding was that they had bad performance?
<a href="http://www.bungie.net/stats/halo3/defau ... player=ALI H IS GREAT"><img src="http://www.bungie.net/card/halo3/ALI H IS GREAT.ashx"></a>
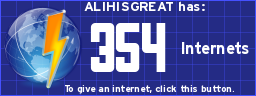
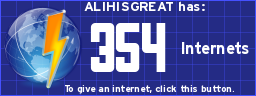
Nope it isnt.BTW: The burst disk is just there in case the valve were to jam and trap the explosion inside the pipes. Cause' that'd be bad
1-The pressure will drop to atmospheric in a few seconds.
2-If your chamber cant handle that pressure for a longer period, it is not safe to use it at those pressures.
3-Remember that shock loading may be even worse.
Also, I'd like to comment the following:
Instead of a spring, I would use air pressure as backforce.
A few bar can exert quite a bit force on the piston/diaphragm and you will need to have one hell of a strong spring to psuh back on that.
- noob of noobs
- Specialist 3
- Posts: 320
- Joined: Tue Jun 12, 2007 8:04 pm
- Location: Illinois, Skokie
@ ALIHISGREAT: Yeah, looking at the search results, hybrid coaxials have bad expected preformance. However, I think I might try it anyways; I'm more concerned with the ROF of the system than the energy. For now I think I'll go with the diahphragm for simplicity, but if I try to improve the system, I'll probably try a diaphragm with a piston attatched to it like on a sprinkler valve to decrease the coaxial aspects of it. I added a diagram to help illustrate:
@ psycix: I'm pretty sure copper and steel make decent hybrid chambers, but I still don't plan on ever taking this higher than a 4X propane mix. Also, I know that a strong spring would be needed to act as a bumper in a piston valve, but are bumpers needed in a diaphragm valve? And since I've never made a decent o-ring seal sucessfully, I'd prefer not to risk fuel getting behind a piston and exploding; hence the diaphragm.
@ psycix: I'm pretty sure copper and steel make decent hybrid chambers, but I still don't plan on ever taking this higher than a 4X propane mix. Also, I know that a strong spring would be needed to act as a bumper in a piston valve, but are bumpers needed in a diaphragm valve? And since I've never made a decent o-ring seal sucessfully, I'd prefer not to risk fuel getting behind a piston and exploding; hence the diaphragm.
- ALIHISGREAT
- Staff Sergeant 3
- Posts: 1778
- Joined: Sat Aug 25, 2007 6:47 pm
- Location: UK
the piston diaphragm should have better performance, but then you still have the problem of the momentum of the piston, it will be interesting to see how it turns out.
<a href="http://www.bungie.net/stats/halo3/defau ... player=ALI H IS GREAT"><img src="http://www.bungie.net/card/halo3/ALI H IS GREAT.ashx"></a>
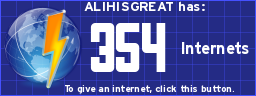
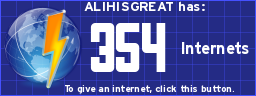
i still say that it will come to a relatively slow stop if you use an air spring and extremely little dead volume. this also lets you choose your opening pressure relatively precisely.
POLAND_SPUD wrote:even if there was no link I'd know it's a bot because of female name